Water Scarcity and Ultraviolet Light for Sterilisation – Integrated Water Reuse Solutions in the UK & Ireland
- paulgueran
- 5 days ago
- 19 min read
Facing Water Scarcity - Integrated water reuse solutions in the UK and Ireland
Water scarcity has become a pressing challenge in the UK and Ireland, driven by climate change, population growth, and aging water infrastructure. Recent hot summers and lower rainfall have led to drinking water shortages and hosepipe bans, highlighting the region’s vulnerability to water stress. The head of the UK Environment Agency even warned that England could run out of water within a few decades without urgent action on conservation and reuse. While Ireland is traditionally wetter, it too faces localised water stress during dry spells and high demand periods. In response, water utilities and industries are exploring innovative water reuse technologies to stretch existing supplies.
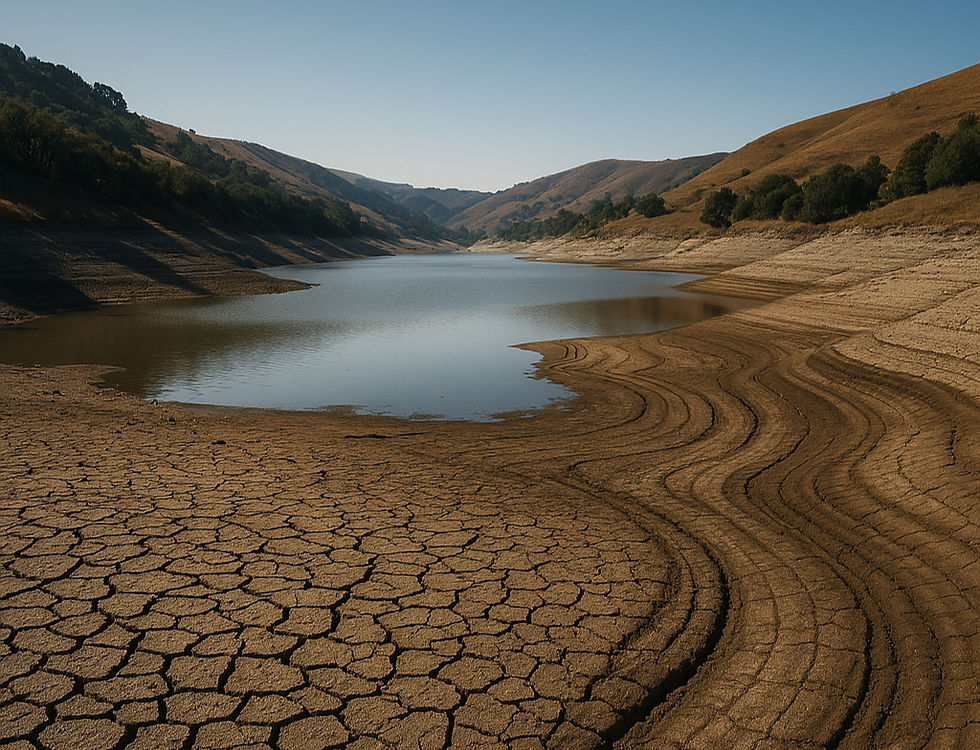
Water reuse (recycling treated wastewater for beneficial use) offers a sustainable way to augment supply. By treating wastewater to a high standard, it can be safely reused for irrigation, industrial processes, and even as part of drinking water sources in indirect potable reuse schemes. This not only eases pressure on freshwater sources but also cuts down the volume of effluent discharged to rivers or coasts. However, turning wastewater into a reliable resource requires overcoming two key challenges: ensuring public health safety and doing so efficiently without excessive energy use. That’s where an integrated, multi-barrier treatment approach comes in – combining advanced purification steps to remove all classes of contaminants while optimising energy consumption.
The Need for Integrated Water Reuse Technologies
Modern water reuse systems employ integrated multi-barrier treatment trains – a sequence of diverse treatment processes, each targeting specific contaminants. No single technology can eliminate all pollutants efficiently, especially the micro-pollutants (trace pharmaceuticals, hormones, pesticides, etc.) and emerging chemicals like PFAS (per- and polyfluoroalkyl substances, also known as “forever chemicals”). By layering multiple barriers, we ensure robust micro-pollutant removal and achieve water quality that meets stringent safety standards.
Crucially, these advanced processes are being designed to minimise energy waste as well. Innovative engineering (like energy recovery devices in membranes technologies and high-efficiency LED UV disinfection units) means that treating and reusing water can have a lower carbon footprint than one might expect. Integrated reuse plants can actually reduce overall energy waste by recovering energy within the process (for example, capturing the pressure from reverse osmosis concentrate) and by avoiding the need to transport water over long distances. In essence, an integrated reuse system not only saves water by recycling it, but can also be optimised to save combined total energy and tCO₂ .
Below, we explore the components of a typical multi-barrier treatment train used in municipal and industrial water reuse applications. Each step plays a vital role in removing contaminants – from suspended solids and organics to dissolved salts, pathogens, PFAS, and trace chemicals – ensuring the recycled water is safe and fit for purpose.
Multi-Barrier Treatment Train for Water Reuse
An effective reuse treatment train often involves the following stages, each acting as a “barrier” to different pollutants:
1. Dissolved Air Flotation (DAF) – Removing Oils and Solids Early
One of the first barriers in many water reuse systems is dissolved air flotation (DAF). DAF is a physical separation process that targets insoluble contaminants like suspended solids, fats, oils, and greases. In a DAF unit, microscopic air bubbles are introduced into the water; these bubbles attach to particulate matter and floating impurities, lifting them to the surface as a foam or sludge layer that can be skimmed off. This process is highly effective at clarifying water that contains algae, colloids, or emulsified oils (common in industrial wastewaters from food processing, petrochemicals, etc.). By removing turbidity and bulk contaminants early, DAF protects downstream processes from fouling and reduces the overall treatment load.
In a municipal context, DAF might be used after initial screening of sewage to remove scum and solids, or in potable water treatment to clarify algae-laden reservoir water. In industrial reuse, DAF is popular for treating wastewater with high grease or solids content. While DAF on its own doesn’t eliminate dissolved pollutants or micro-pollutants, it creates a cleaner feed water for subsequent steps. This improves the efficiency of filters and membranes by preventing clogging and can even help capture some hydrophobic organic compounds that adhere to the floated sludge. By tackling water contaminants like oils and suspended solids upfront, DAF contributes to both water reuse reliability and energy efficiency (a cleaner feed means lower energy demand in later filters).
2. Membrane Bioreactor (MBR) Systems – Biological Treatment with Filtration
After DAF (or sometimes in place of it, depending on the water quality), a Membrane Bioreactor (MBR) is commonly employed to degrade organic pollutants and remove remaining suspended solids. An MBR combines conventional biological wastewater treatment (the kind that uses microbes to consume organic matter) with membrane filtration. In an MBR bioreactor, beneficial bacteria and other microorganisms break down biodegradable impurities – for example, consuming sewage organics, ammonia, and even some pharmaceutical residues. What makes an MBR different from a normal treatment plant is that instead of a settling tank to separate treated water from biomass, it uses a membrane filter (microfiltration or ultrafiltration membranes) to strain out all solids, including the bacteria themselves.
This results in an extremely clear effluent with very low turbidity and significantly reduced organic content. Many micro-pollutants are partially removed here: some are biologically degraded by the microbes, and others get adsorbed onto the biomass or filtered out with the sludge. The term membrane bio reactor highlights this synergy of biology and filtration. Modern MBR bioreactor systems are widely used in water reuse because they produce a consistently high-quality effluent that serves as an ideal feed for the next purification steps. The membranes typically have pore sizes in the ultrafiltration range (0.01–0.1 micron), which means even most bacteria and some viruses are physically removed at this stage, in addition to the biological treatment of dissolved organics.
From an energy standpoint, MBRs can be somewhat energy-intensive (due to aeration for the microbes and pumping/ drawing through membranes), but they often replace multiple steps (primary clarification and secondary clarification in a conventional plant, plus separate media filtration) with one compact unit. As a result, MBRs have become a standard in cutting-edge reuse water treatment trains, especially where space is at a premium or high effluent quality is required (such as direct potable reuse pilots).
3. Ultrafiltration (UF) Pre-Treatment – Polishing and Protecting Downstream Processes
If a Membrane Bioreactor is not used, or if further polishing is desired, ultrafiltration (UF) membranes serve as a next barrier. UF is a pressure-driven membrane filtration process that removes any remaining fine particles, colloids, and microbes. In many reuse schemes, either an MBR or a conventional biological treatment followed by UF is used – the goal in both cases is to produce very low-turbidity water before advanced treatment. UF membranes typically have pore sizes around 0.01–0.1 micron, which effectively blocks bacteria, protozoa, and to a large extent viruses, while letting dissolved salts and organics pass through.
In a train where an MBR was used (and thus already has membrane filtration), an additional UF might not be necessary. However, some systems still include a separate UF step to ensure absolutely no suspended solids carry over, especially if the MBR used slightly larger-pore membranes or if there’s a risk of membrane integrity issues. In other designs, a plant might use a conventional activated sludge (no membrane) and then rely on ultrafiltration as a distinct step to do the solid-liquid separation. Either way, by the time water has passed through UF, it is typically free of any particulate matter and most microorganisms.
This clarity is important for the next stage – reverse osmosis filtration – because RO is very sensitive to fouling from particles. Also, having UF as a barrier means the downstream UVT for ultraviolet light for sterilisation (disinfection) will be higher since UV transmittance is low in low-turbidity water. In summary, UF ensures robust physical removal of pathogens and safeguards the high-tech membranes that follow. It is a chemical-free process (just physical separation), aligning well with the push for chemical-free water treatment solutions in reuse.
4. Reverse Osmosis (RO) Filtration – Removing Dissolved Salts and PFAS
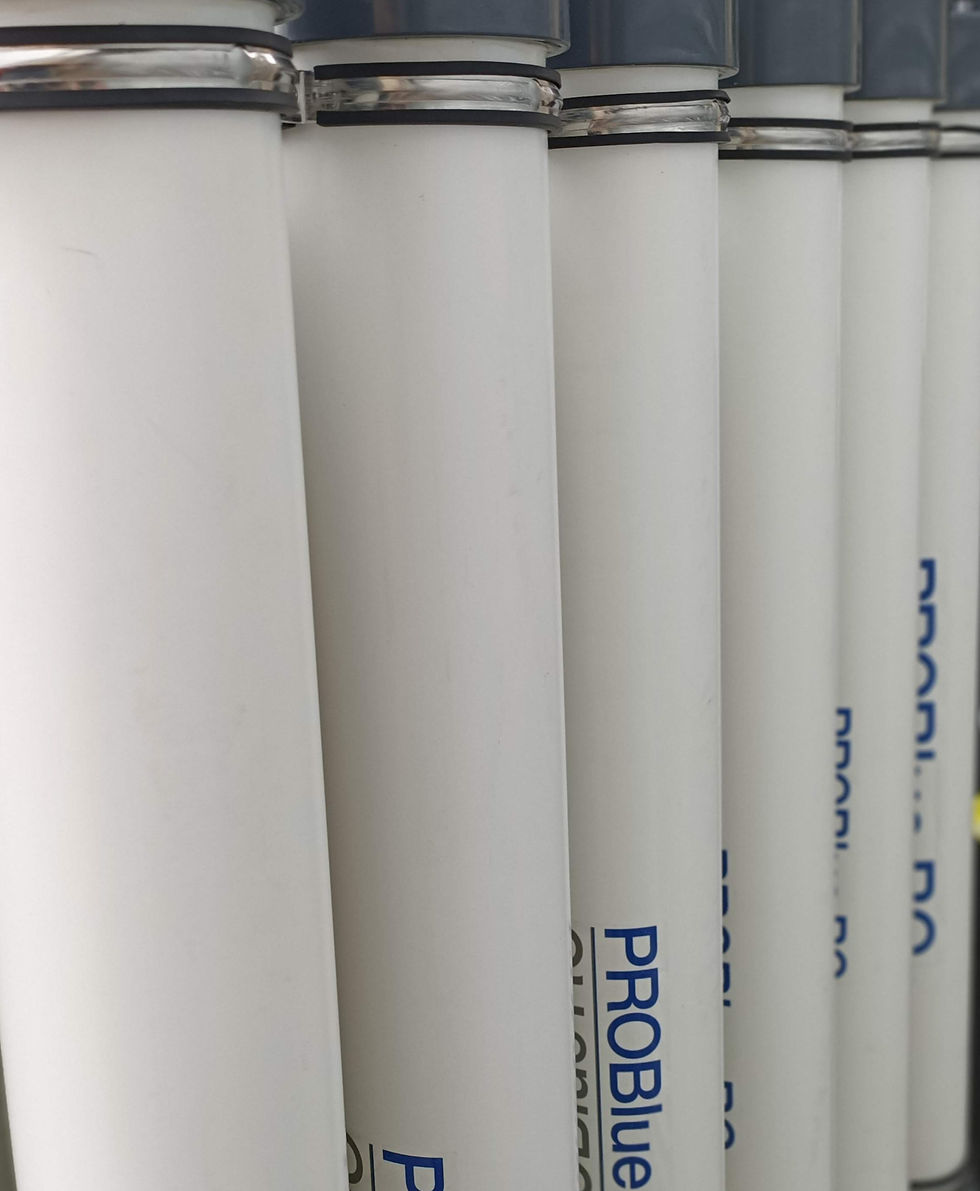
Reverse osmosis filtration is often considered the heart of an advanced water reuse train. RO is a membrane technology that pushes water through an extremely tight semi-permeable membrane, allowing only pure water molecules (and a very small fraction of other very light molecules) to pass, while rejecting the vast majority of dissolved solids. This includes salts (desalination), heavy metals, nutrients like nitrate, and a broad range of organic molecules. In the context of water reuse, RO serves multiple crucial functions:
Desalination and Softening: It removes minerals and salts, which is essential if the recycled water is to be used for industrial processes (e.g., in boilers or cooling systems) or for potable purposes (to meet drinking water standards for salinity). Many inland regions have brackish groundwater or accumulate salts in wastewater; RO ensures the reused water is not too saline.
Micro-pollutant Removal: RO membranes have high rejection rates for most micro-pollutants such as pharmaceutical residues, pesticides, personal care product chemicals, and endocrine disruptors. These are often molecules larger than water and carry some charge or hydrophobicity that makes them likely to be filtered out. While not every single molecule is 100% rejected, RO typically removes 90%+ of many trace organic contaminants, providing a huge reduction before the next stage.
PFAS Treatment: PFAS, the notorious “forever chemicals” found in firefighting foams, non-stick coatings, and industrial discharges, are a growing concern in water supplies. These compounds are difficult to break down chemically, but RO is one of the effective barriers to them. PFAS treatment via RO works because PFAS molecules (like PFOA, PFOS) are larger than water and often exist as charged ions; a well-designed RO system can reject a high percentage of PFAS, significantly lowering their concentrations in the product water. The downside is that PFAS and other contaminants concentrate in the RO reject (brine), which then requires careful disposal or further treatment (more on that later).
Reverse osmosis, however, is energy-intensive, as it requires high pressure to drive water through the membrane. To address energy waste, modern RO systems in large reuse plants often incorporate energy recovery devices and operate at optimised pressures. These improvements have made RO more sustainable, even for wastewater reuse applications. In the UK and Europe, there is growing interest in low-pressure RO and innovative designs to reduce energy costs while maintaining high removal efficiency.
After RO, the water is essentially very pure – low in organics, salts, and most chemicals. Yet, a few challenges remain: any trace organic that might have slipped through, the presence of dissolved gases, and the fact that the water is now devoid of minerals (if intended for potable use, minerals might be reintroduced for taste and corrosion control). Additionally, we must deal with the concentrated waste (the RO concentrate) which contains all the removed contaminants in smaller volume – including PFAS, which often necessitates further handling like high-temperature incineration or advanced waste treatment to avoid environmental release.
5. Advanced Oxidation Processes (AOPs) – Destroying Resistant Micro-Pollutants
To further address any trace organic chemicals that might remain after RO (or in cases where RO is not used, to tackle dissolved contaminants directly), Advanced Oxidation Processes (AOPs) are employed. AOPs are a set of chemical treatment methods designed to generate highly reactive radicals (especially the hydroxyl radical •OH) that can oxidize and break down persistent organic molecules into smaller, harmless end products (ideally into carbon dioxide, water, and inorganic ions). They are extremely useful for destroying micropollutants that are resistant to conventional biological treatment or that may pass through RO.
One of the most common AOPs in water reuse is UV/H₂O₂, which involves adding hydrogen peroxide to the water and then exposing it to ultraviolet light. The UV energy catalysis the decomposition of hydrogen peroxide into hydroxyl radicals. These radicals then attack organic pollutant molecules, rupturing chemical bonds. Deep ultraviolet light (UVC) is thus leveraged not only to inactivate microbes but also to initiate chemical reactions that oxidize micro-pollutants. For example, UV/H₂O₂ can help break down trace pesticides, NDMA (an undesirable disinfection by-product), pharmaceutical residues, and many industrial organic chemicals into less harmful substances.
Other AOPs include ozone combined with peroxide (O₃/H₂O₂) or photocatalysis (UV with a catalyst like titanium dioxide). The choice depends on the contaminants of concern and operational practicalities. In reuse systems, UV/H₂O₂ has been popular because it provides a double benefit: disinfection and oxidation in one step (with UV taking on the dual role). It’s worth noting that while AOPs are powerful against many organics, certain extremely stable compounds like PFAS may only be partially oxidized by typical AOPs – complete PFAS removal may require other specialised treatments. Thus, AOP is usually targeting the non-PFAS micro-pollutants (and some precursors to disinfection by-products).
By integrating an AOP step, the treatment train ensures that even trace contaminants that slipped past RO (or that are present if RO isn’t used) are dealt with. This is particularly important for potable reuse projects, where the public needs assurance that the water is free from even minute levels of harmful chemicals. AOPs are considered a chemical-free water treatment in the sense that they don’t leave any residual chemicals in the water (hydrogen peroxide breaks down into water and oxygen, ozone reverts to oxygen). They do, however, consume chemicals and energy in the process, so they must be carefully controlled for cost-effectiveness.
6. Activated Carbon Filtration (GAC) – Adsorbing Residuals and Protecting Downstream
After an AOP step, it is common to include an activated carbon filtration stage. Granular Activated Carbon (GAC) is a form of carbon with a highly porous structure and large surface area, ideal for adsorbing organic molecules. Placing carbon after AOP is strategically ideal for a number of reasons:
Adsorption of AOP By-products: AOP can sometimes break complex micro-pollutants into smaller organic fragments. If not fully mineralized to CO₂, these fragments might still be present as minor contaminants. GAC can capture these remaining molecules, polishing the water to pristine quality. Additionally, AOP of some substances (like certain pesticides or organic compounds) could produce intermediate by-products that we’d prefer not to let through; carbon will adsorb many of these.
PFAS Capture: GAC is a key tool for PFAS treatment, especially effective for longer-chain variants like PFOA and PFOS. These compounds are not reliably destroyed by AOP but can be physically adsorbed onto carbon media. GAC’s effectiveness for PFAS depends on factors such as water quality, flow rate, PFAS speciation, and contact time. Once the carbon becomes saturated, it must be replaced or regenerated to prevent breakthrough.
Quenching of Oxidants: Following UV/H₂O₂, there might be some residual hydrogen peroxide in the water. Activated carbon can help decompose and remove residual peroxide (acting as a catalyst to break it down). Similarly, if ozone was used in an AOP, carbon filters are often used after ozonation to remove any residual ozone or by-products like bromate.
Extending Carbon Life: If GAC were placed before AOP, it would take the full brunt of all organic contaminants, quickly exhausting its adsorption capacity. By using AOP first to destroy a large fraction of contaminants, the carbon filter sees a much lighter load. This greatly extends the media life of the carbon. In other words, the carbon lasts longer and doesn’t need to be replaced or regenerated as frequently, which saves on operating costs.
Activated carbon is particularly good at removing taste and odour compounds too, which is beneficial if the water is for potable use (ensuring no funny odours from any trace chemicals). It also adsorbs any remaining micro-pollutants that might have escaped previous steps. For industrial reuse, carbon filters ensure that product water doesn’t carry organics that could interfere with processes or product quality (for instance, in food & beverage industries).
Spent Carbon Management: One important consideration with GAC is what happens when the carbon media is exhausted (saturated with contaminants). Two main options are common:
Reactivation/Incineration: Spent carbon can be sent to high-temperature facilities to be thermally reactivated. Essentially, the carbon is heated in a controlled way to burn off the adsorbed organics, restoring much of the carbon’s capacity, and then it can be reused. In cases where the adsorbed contaminants include hazardous substances (like PFAS or certain industrial chemicals), the process typically needs to be a full incineration at very high temperatures to destroy those contaminants. Incineration is often the preferred method for PFAS-laden carbon, because simple landfill disposal could lead to PFAS leaching out into the environment. High-temp incineration (above ~1100°C) can break the strong carbon-fluorine bonds in PFAS, effectively destroying them.
Landfill (avoid if possible): Historically, some spent carbon (especially from water treatment containing everyday organics) might be sent to landfill. However, this is becoming less acceptable, particularly if the carbon contains PFAS or other persistent toxins that could leach. Given PFAS are “forever chemicals,” landfilling contaminated carbon is essentially delaying the problem and risking pollution down the line. Thus, environmental best practice is trending towards regenerating or incinerating spent carbon instead of landfilling it.
In summary, activated carbon acts as a safety net and finishing step in the treatment train, ensuring the highest possible water quality. It’s a proven industrial carbon filter technology used in both municipal water plants and industries (for example, in food and beverage water polishing or pharmaceutical water systems) due to its broad-spectrum adsorption capabilities. By the time water has passed through AOP and GAC, it is typically free from detectable levels of organic pollutants.
7. Deionisation (DI) for Final Polishing – Removing Remaining Ions if Needed
Depending on the end-use of the recycled water, a Deionisation (DI) step may be included near the end of the train. Deionisation usually refers to ion exchange processes that remove remaining dissolved ionic species from water. In many cases, after RO and the above processes, the water is already very low in ions. However, certain high-purity applications (such as electronics manufacturing or power plant boiler feed water) might require almost zero hardness, silica, or specific ion contaminants. A mix-bed ion exchange resin (commonly called a DI column) can polish the water to ultra-pure levels, capturing trace ions that RO didn’t remove.
For instance, if the reuse water is intended for a district heating system or a high-pressure boiler, even a few parts per million of hardness minerals could cause scaling. A DI unit would ensure those are removed. In a potable reuse scenario, DI is less common, since it would strip away minerals that are actually beneficial for human consumption and corrosivity control; instead, potable reuse systems often add minerals back. So DI is typically an optional step more relevant to industrial reuse where water purity standards are extremely high.
It’s worth noting that ion exchange resins have to be regenerated with chemicals (acid and caustic) once they become saturated with captured ions, which introduces a chemical handling aspect to the system. Some modern plants avoid DI by using a second-pass RO or other polishing steps to remain chemical-free. But we mention DI here as it is one tool in the toolbox for achieving the desired water quality, especially for industrial clients needing demineralised water.
8. Ultraviolet Disinfection with LED UV-C Systems – Final Barrier Protection

As the final step (or one of the final barriers) in an integrated reuse train, ultraviolet disinfection is employed to inactivate any remaining pathogens. Even after all the previous treatments, it’s prudent to have a strong disinfection barrier before the water is distributed for use. Bacteria, viruses, or protozoa could potentially enter the water upstream of the UV (through tiny leaks or during storage), or trace levels that passed through RO (especially viruses, which are the smallest) need a final kill step. UV disinfection is ideal here because it’s fast, effective, and doesn’t leave chemical residues.
UV-C LED systems represent the cutting edge in UV disinfection technology. Traditional UV systems use mercury-vapor lamps, but LED UV disinfection systems like the LED UV-C Kilo and Tera models (offered by LED UV-C Systems Ltd) use light-emitting diodes to generate germicidal UV light. These LEDs emit UV-C light (around 260–280 nm wavelength) which damages the DNA and RNA of microorganisms, rendering them unable to reproduce (effectively sterilizing them).
Key advantages of LED UV-C disinfection systems for modular UV water disinfection in reuse applications include:
Immediate On/Off and Modularity: LED UV units reach full intensity instantly and can be turned on/off as needed, which is perfect for variable flow operations. This on-demand nature can save energy (no need to keep lamps on constantly). They are also inherently modular – systems like the Kilo and Tera can be scaled by adding multiple LED modules in parallel to treat larger flows. This modularity is attractive for designing disinfection systems for both medium and large centralised plants, as you can add capacity as needed or build in redundancy easily.
Chemical-Free Disinfection: UV is a physical disinfection method – it introduces no chemicals into the water, unlike chlorination or ozonation. This means no formation of disinfection by-products like trihalomethanes, and no need to remove chemicals later. For facilities aiming for chemical-free water treatment, LED UV is an excellent choice. (In cases where a residual disinfectant is needed in distribution, a small chlorine or chloramine dose might be added after UV, but the heavy-lifting of pathogen kill is done by UV).
Safety and Maintenance: LED UVC systems contain no mercury lamps, eliminating the risk of mercury exposure or special handling requirements at end-of-life. LEDs also have long lifespans and degrade gradually, and they’re robust against frequent cycling. Maintenance is typically simpler – modules can be replaced easily, and there isn't a high number of fragile quartz sleeves that need careful replacement or cleaning. The Kilo and Tera units, for example, are designed for low maintenance and reliable performance in industrial environments.
Support for AOP: These high-output UV systems can also double up to support UV/H₂O₂ AOP treatments as described earlier. By injecting hydrogen peroxide upstream of the UV unit, the same disinfection system can generate advanced oxidation for micro-pollutant destruction. This dual functionality means an LED UV reactor can be a multi-purpose barrier: sterilising microbes and breaking down chemical pollutants simultaneously, without needing separate reactors.
Ultraviolet water disinfection thus serves as a final barrier to protect public health. In reuse schemes aimed at potable water augmentation, UV is often the last step before the water enters a reservoir or water supply network. In industrial water reuse, UV ensures that water fed into a process or cooling system won’t introduce microbial growth. With water scarcity driving the adoption of reuse, having ultraviolet light for sterilisation gives regulators and the public confidence that even trace bacteria or viruses are neutralised in the recycled water.
Real-World Applications and Benefits of Multi-Barrier Reuse
Multi-barrier water reuse trains like the one described are not just theoretical – they are in use around the world, showcasing impressive results in terms of both water savings and safety:
Singapore’s NEWater: Singapore, a country known for water scarcity and drinking water shortages due to limited natural resources, has implemented NEWater – a reclaimed water supply – on a large scale. The process employs microfiltration, reverse osmosis, and ultraviolet disinfection, similar to what we’ve outlined. The result is ultra-clean water that is fed into reservoirs and used by industries, reducing the nation’s dependence on imported water. Singapore’s success with reuse has demonstrated that even wastewater can be turned into a reliable drinking water source with the right technology and monitoring.
Orange County, California: Home to one of the world’s largest potable reuse projects, Orange County’s Groundwater Replenishment System takes treated wastewater and purifies it through a three-step process (microfiltration, RO, UV/H₂O₂). The purified water is then injected into groundwater aquifers, effectively expanding drinking water supplies. This system has operated for over a decade, producing up to 100 million gallons per day of water, and stands as a proof of concept that multi-barrier advanced treatment (including ultraviolet light with hydrogen peroxide for AOP) works at scale to alleviate water stress in drought-prone regions.
Industrial Reuse in Europe: Across Europe, industries are adopting water reuse to cut their freshwater intake and improve sustainability. For example, some large food and beverage factories and textile plants use on-site reuse plants incorporating DAF, biological treatment, RO, and UV to recycle process water. These systems help companies ensure a resilient water supply for operations even during regional shortages. In one case, a brewery in Belgium turned its wastewater into process water using a multi-barrier system and even produced a beer from recycled water to demonstrate the quality. European regulations (such as the EU’s new water reuse standards) and tightening discharge limits for micro-pollutants are encouraging more such installations, and technologies like PFAS treatment are becoming crucial as the EU and UK set stricter limits on PFAS in water.
UK Water Companies’ Initiatives: While historical reliance on reservoirs and rainfall has been accepted, recent droughts have accelerated interest in integrated water reuse solutions in the UK. Thames Water and other utilities have considered schemes to pipe highly treated wastewater into upstream reservoirs or rivers (a form of indirect potable reuse) to bolster supplies during dry weather. Any such scheme would use the kind of multi-barrier approach described: e.g., taking effluent from a wastewater plant and further treating it with UF, RO, UV, and GAC before release. Though at pilot stages, these plans indicate a strategic shift toward reuse as a tool to fight water scarcity. Additionally, many UK industries (power plants, manufacturing) already recycle water internally, using RO and advanced filtration to reuse cooling water or rinse water and thus reduce overall abstraction.
The benefits of integrated water reuse are compelling:
Reliable Water Supply: By recycling water, communities and businesses gain an extra, drought-proof source of water. This improves resilience against climate variability.
Environmental Protection: Less freshwater extraction means more water stays in natural ecosystems (rivers, aquifers), and lower wastewater discharge means reduced pollution load on those ecosystems. Also, removing micro-pollutants and PFAS in reuse plants prevents these from continually cycling in the environment.
Energy and Cost Savings: Although advanced treatment requires energy, it can be offset by efficiency gains and by the fact that delivering water locally may use less energy than pumping from afar. Using energy recovery devices, efficient reverse osmosis filtration designs, and UV-C LED systems, modern reuse plants aim to keep energy per volume treated as low as possible. Over time, the cost of reuse water has been dropping, and in water-scarce areas it is now often cheaper than alternatives like desalinating seawater or transporting water long distances.
Public Health Safeguards: The multi-barrier approach is all about safety through redundancy. Even if one step under-performs briefly, the subsequent steps ensure that pathogens or chemicals do not get through. For example, if RO has a slight issue, the UV and AOP can neutralise what passes. This layered safety is why regulators are increasingly comfortable with potable reuse. Additionally, by incorporating LED UV water disinfection as a final step, these systems ensure water is free of bacteria and viruses without needing heavy chlorine doses, which is great for water taste and avoids harmful by-products.
Conclusion: Toward a Sustainable Future with Water Reuse and LED UV Sterilisation
Water scarcity is no longer a distant worry for the UK and Ireland – it’s a current reality that demands innovative solutions. Integrated water reuse technologies offer a pathway to water security by turning waste into a resource. By combining processes like DAF, MBR, UF, reverse osmosis filtration, AOP, carbon industrial carbon filters, DI, and ultraviolet light for sterilisation into a cohesive treatment train, we can produce water that is pure and safe for almost any use. This multi-barrier strategy mirrors nature’s own cleansing (multiple steps of filtration and degradation) but in a controlled, accelerated manner.
LED UV-C Systems Ltd’s LED UV disinfection units (such as the Kilo and Tera) exemplify how modern technology is making these systems more efficient and sustainable. UV-C LEDs provide powerful disinfection in a modular, energy-savvy package, and support advanced oxidation for breaking down stubborn pollutants – all without adding chemicals to the water. This aligns perfectly with the needs of both municipal reuse schemes and large industrial water recycling installations in the UK, Ireland, and worldwide.
In embracing water reuse, communities can reduce water waste (by recycling every drop) and also address energy waste by implementing energy-efficient technologies at each step. Every stage from flotation to UV can be optimised for lower power consumption, and the net effect is often positive when considering the energy that would be used to obtain new water elsewhere. Moreover, tackling issues like PFAS treatment and micro-pollutant removal in reuse systems means we are not only securing water quantity but also improving water quality for future generations.
The trend is clear: water-stressed regions around the globe are investing in water reuse solutions, and the UK and Ireland are well placed to adopt these proven technologies. By implementing robust, multi-barrier treatment strategies and sharing transparent information about water quality and safety, we can strengthen public confidence in recycled water. Clear communication around protective technologies – such as LED ultraviolet light for sterilisation acting as a final safeguard – helps reinforce the integrity of reuse systems and builds trust among users, regulators, and communities.
In embracing water reuse, we reduce pressure on natural resources, cut water and energy waste, and create more resilient systems that support public health, industry, and environmental protection. As climate variability continues to challenge water availability, these adaptable, technology-driven solutions offer a sustainable path forward – not only for managing water scarcity, but for shaping a smarter, more secure water future.
Take the Next Step Toward Sustainable Water Reuse
Whether you’re designing a new treatment train or upgrading existing infrastructure, integrating high-efficiency technologies like LED ultraviolet light for sterilisation can add measurable value — improving performance, reducing operational costs, and supporting sustainability goals. At LED UV-C Systems Ltd, we provide specialist expertise in UV-C LED technology for advanced water disinfection and AOP applications, tailored for municipal and industrial reuse scenarios across the UK and Ireland.
Get in touch to explore how our Kilo and Tera UV-C LED systems can support your water reuse project — and help build a more resilient, low-carbon future for water.
👉 Contact Us | 📩 sales@leduv-c.co.uk | 🌐 www.leduv-c.co.uk
Comments